For over 50 years, TMC has specialized in providing precision working surfaces and vibration isolation systems for precision measurement laboratories and industry. To provide optimal performance, both precision “
tops” and their
supporting isolators must be designed to address the central issue: control of environmental noise.
To learn more about table tops, please
visit this page.
1. Sources of Vibration (Noise)
There are three primary sources of vibration (noise) which can disturb a payload: ground vibration, acoustic noise, and “direct force” disturbances. Ground or seismic vibration exists in all environments throughout the world. This noise has various sources, from waves crashing on coastal shorelines, the constant grind of tectonic plates, wind blowing trees and buildings, to manmade sources like machinery, HVAC systems, street traffic, and even people walking. TMC vibration isolation systems are designed to minimize the influence of these vibration sources.
To learn more about active vibration isolation systems, please
visit this page.
Acoustic noise comes from many of the same sources but is transmitted to the payload through air pressure waves. These generate forces directly on the payload. Even subsonic acoustic waves can disturb a payload by acting as a differential pressure on the diaphragms of pneumatic isolators. Air currents generated by nearby HVAC vents can also be a source of “acoustic” noise. TMC manufactures
Acoustic Enclosures for OEM applications which protect payloads from this type of disturbance by providing a nearly airtight, heavy, energy-absorbing enclosure over the entire payload.
Acoustic noise can be measured, but its influence on a payload depends on many factors which are difficult to estimate (such as a payload’s acoustic (
cross-section). The analysis of this type of noise source goes beyond the scope of this discussion.
* In general, acoustic noise is the dominant noise source of vibration above 50Hz.
The third source of vibration is forces applied directly to the payload. These can be in the form of a direct mechanical coupling, such as vibration being transmitted to the payload through a hose, or a laser water cooling line. They can also come from the payload itself. This is the case in semiconductor inspection equipment, where moving stages are used to position silicon wafers. The force used to accelerate the stage is also applied to the “static” portion of the payload in the form of a reaction force. Moving stages also shift the payload’s overall center-of-mass (COM). Reducing these sources
of vibration can be done passively, with TMC's MaxDamp line of isolators or actively using feedback or feedforward techniques. Payload-generated noise sources are usually of a well-known nature and do not require any measurements to characterize.
The influence of vibration transmitted to the payload can be minimized through good payload design. TMC offers a wide range o
f honeycomb optical tables, breadboards, and platform laminations. These are available in standard and custom shapes and sizes. All reduce the influence of environmental noise by having high resonant frequencies and exceptional damping characteristics.
For more information about pneumatic isolators, please
visit this page.
1.1 Measuring Noise
Seismic (floor) noise is not usually known in advance and must be measured. There are two types of seismic noise sources: periodic or coherent noise and random or incoherent noise. The first requires the use of an
amplitude spectrum while the second is analyzed using an
amplitude spectral density. To determine the expected levels of vibration on a payload, these must be combined with the vibration transfer function for the isolation system supporting it.
1.1.1 Periodic Noise
Periodic noise usually comes from rotating machinery. By far the most common example is the large fans used in HVAC systems. These fans spin at a constant rate and can generate a continuous, single-frequency vibration (and sometimes several harmonic frequencies as well). Another common source is air compressors. Unlike building fans, these cycle on and off according to demand. Compressors should be considered periodic, coherent noise sources, though they are
nonstationary, meaning a measurement will change depending on whether the source is active or not. All periodic noise sources should be measured using an amplitude spectrum measurement, whether they are stationary or not.
An
amplitude spectrum measurement is produced by taking the
Fourier transform of data collected from a sensor measuring the noise. The most common sensor is an accelerometer, which will produce a spectrum with units of
acceleration as a function of frequency. Accelerometers are popular because they have a “flat” frequency response, and random ground noise is usually fairly “flat” in acceleration (see section 1.2.2 below). Amplitude spectrums can also be expressed as velocity or position amplitudes as a function of frequency. Most spectrum analyzers use the Fast Fourier Transform, or FFT. An FFT analyzer finds the amplitude of each frequency in the input data and plots it. This includes the amplitudes and frequencies of any periodic noise sources. The amplitudes of periodic noise sources measured using an amplitude spectrum are independent of the length of the data record.
1.1.2 Random Noise
Random, or incoherent noise, is measured using an
amplitude spectral density. The difference is that the amplitude spectrum (above) is multiplied by the square root of the data record’s length before being displayed by the analyzer. The result is a curve which measures the random noise with units of [units] /

, where [units] may be acceleration, velocity, or position. This
normalization for the
measurement bandwidth ensures that the measured noise level is independent of the length of the data record. ** Without making this correction, for example, the level of random noise would appear to decrease by a factor of ten if the length of the data record were increased by a factor of 100. Note that periodic noise sources will appear to grow in amplitude as the data record gets longer when using the spectral density. Random ground noise levels vary greatly, but an “average” site may have 0.5 µg / √ Hz of noise between 1 and several hundred Hz. Random noise can also be nonstationary. For example, stormy weather can significantly increase levels of random seismic noise. Figure 1 illustrates common noise levels in buildings.***
1.1.3 Measuring RMS Values
Since most locations have a combination of both random and periodic noise sources, it is often desirable to come up with a single number which characterizes noise levels. This is usually done by quoting an RMS (Root-Mean-Squared) noise level within a specified range of frequencies. Fortunately, this is easily done by integrating the power spectral density or PSD over the frequency range of interest. The PSD is the square of the amplitude spectral density. This gives the following expression for the RMS motion between the frequencies f
1 and f
2
This formula correctly calculates the RMS value of the measurement taking into account both periodic and random noise sources. Most spectrum analyzers are capable of performing this integration as a built-in function. The contribution to this RMS value from any single periodic source can be measured using the amplitude spectrum (
not the amplitude
density) and dividing the peak value by √2. The contribution from several peaks can be combined by adding them in quadrature. RMS values are also sometimes expressed in “1/3 octave plots” in which a histogram of the RMS values calculated in 1/3 octave frequency bins is displayed as a function of frequency. An octave is a factor of two in frequency.
1.1.4 Characterizing Isolators
The noise level on a payload can be predicted by measuring the ground noise as described above, then multiplying those spectra by the transfer function for the isolation system. The
transfer function is a dimensionless multiplier specified as a function of frequency and is often referred to as the isolator’s
transmissibility. It is typically plotted as the ratio of table motion to ground motion as a function of frequency. It is common to express transmissibility in terms of decibels, or dB:
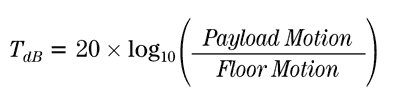
In practice, measuring the transfer function for an isolation system can be corrupted by other noise sources acting on the payload (such as acoustic noise). This is the primary reason why many measured transfer functions are noisy. To improve the quality of a transmissibility measurement, a “shake table” can be used. This is dangerous, however, as it can misrepresent the system’s performance at low levels of vibration. The transfer function for pneumatic isolators is discussed in Section 2.0.
To learn more about how isolators work, please
visit this page.
* See Cyril M. Harris, Ed., Shock and Vibration Handbook, Third Ed. (The McGraw-Hill Companies, 1987)** Other normalizations often apply such as corrections for “data-windowing” which is beyond the scope of this text. See “The Fundamentals of Signal Analysis,” Application Note Number 243. Hewlett Packard Corporation.
*** Reprinted with permission from Colin Gordon Associates. VCA–VCE refer to accepted standards for vibration sensitive tools and instruments. The levels displayed are RMS values measured in 1/3 octave band center frequencies.