Serial vs. Parallel Type Active Systems in Vibration Cancellation Applications
As the demands placed on nanoscale metrology and manufacturing equipment trend toward higher resolution, smaller tolerance, and faster throughput, the need to provide adequate vibration isolation presents an increasingly important and complicated challenge, particularly at very low frequencies. Many users have begun to favor active vibration cancellation systems, which incorporate the use of sensors, actuators, and control algorithms to detect and mitigate vibration. The basic architecture of an active system can be characterized as one of two types: a serial type active system or a parallel type active system.
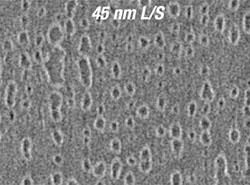
SEM image of nanolithography pattern created with severe low frequency floor vibration present. Photo courtesy of SEMATECH.
SEM image of the same lithography tool, when supported by a serialtype active vibration cancellation system. Photo courtesy of SEMATECH.
Parallel type systems
The first type of active vibration cancellation system developed was the parallel type system, which is still used widely today. Starting with an existing simple, mass-spring-damper passive vibration isolation system, a parallel active system is created by adding a vibration sensor to the payload and applying a cancellation force through an electro-mechanical actuator to damp any residual motion of the payload that has not been isolated by the passive isolation system.
The basic system architecture uses a passive isolator, typically a damped spring, in parallel with an electromechanical actuator, each of which acts simultaneously on the payload (Fig. 1). The passive isolator in most parallel type commercial systems is typically an elastomer mount, a metal die spring, or a pneumatic isolator, and the electromechanical actuator is typically a linear motor (or voice coil motor). The location of the inertial vibration sensor in a parallel type system is important. Some early parallel type systems utilized a ground motion sensor to sense ground position, and delivered a feedback signal to the linear motor to apply an out of phase countering force to the payload in an attempt to cancel the detected vibration. This helped to track response to earth motion, but the dual-sensor method has two inherent limitations.
The first limitation is that the system cannot track information from two sensors at the same time at low frequencies. If there’s a need to cancel out a disturbance at 2Hz on the payload, the gain of the payload sensor must be raised, but the gain of the sensor on the earth must be lowered. Also, any resonances from the passive isolators (which, in the case of most pneumatic isolators, is around 2Hz) are added to the gain of the whole system. The result is a very high sensor gain at the payload at 2Hz, which requires a de-tuning of the ground sensor to the point where it is ineffective at sensing low frequencies.
The second limitation: using feedback sensing of the payload results in all payload resonances being fed into the control loop of the cancellation system. The actuators, in response to the signal from the payload sensor, will incorrectly try to counteract these payload resonances, leading to an unstable system. The alternative is to “de-tune” the system to ensure stability but often to an extent that no significant vibration cancellation is achieved.
At frequencies above 3Hz, bandwidth limitations on sensors play less of a role in the performance of parallel type active cancellation systems. Using modern digital controllers, parallel type systems can be carefully tuned to counteract specific resonances on the floor above 3Hz, but it has been found that tuning to specific frequencies is a highmaintenance activity. As facility conditions change (Fig. 2), frequent re-tuning of a parallel type system is a reality of system ownership.
Given the limitations of parallel type systems at low frequencies, designers sought a more effective use of parallel type systems, which takes advantage of their ability to be tuned to very accurately counteract motion on the payload (but not the floor). This use was found in the application of parallel type systems in feedforward control configurations, which apply a pre-programmed signal to the linear motors to provide a corrective force to the payload based on a known and predictable payload motion.
The application of feedforward parallel style systems to cancelling of on-board motion is well suited for settling-time critical applications, such as cancelling the payload motion caused by a moving stage in a semiconductor inspection tool. In stage motion cancellation, the need for a payload to stop resonating and “settle” to its original position quickly after a stage motion is critical in maximizing inspection throughput in semiconductor manufacturing processes. The feedforward input is known, since the stage position, velocity, and mass are known and constant, and the appropriate cancellation signal can be fed-forward to the actuators in order to cancel out the predicted payload disturbances. Using powerful linear motors, settling times after stage motion can be reduced from seconds to hundreds of milliseconds or less, and throughput can be significantly increased. The use of parallel type feedforward active cancellation systems in this configuration, however, does nothing for cancellation of floor vibration, and therefore must often be used in conjunction with a separate floor vibration cancellation system. Due to the limitations of parallel type systems in cancellation of low frequency floor vibrations, their inherent coupling to payload resonances, and their strengths in feedforward stage motion cancellation, the way to maximize the payback from a parallel type system is to use it in settlingtime critical applications, and rely on a different approach to for floor vibration cancellation.
Serial type systems
A serial type vibration cancellation system places the passive element in series with the active element, and the two are separated by an intermediate mass that is small relative to the payload (Fig. 3). The transfer function of a serial type system is a sum of the transfer functions of both the active element and the passive element, and it is important to note that the intrinsic resonance of each element contributes to the overall isolation performance of the system. Therefore, there must be a significant difference in stiffness between the two components such that their transfer functions may sum, but the components do not couple and oscillate (Fig. 4). A stiff elastomer mount with resonant frequency of 15-20Hz can be employed in series with a piezoelectric transducer as the active actuator, which will have a stiffness value over 100 times greater than the elastomer, resulting in a sufficient resonance separation to ensure no coupling between the passive (elastomer) and active (piezoelectric) elements. For vibration cancellation, the most effective serial type systems always employ a closed loop feedback system, where the inertial vibration sensor is placed on the intermediate mass, and the signal detected is filtered and fed back to the piezoelectric actuator, so it may expand or contract with a displacement of reverse phase to the detected signal. Piezoelectric transducers are uniquely suited to achieve very low frequency performance because of their stiffness and response and can achieve vibration cancellation.
The main design features of a serial type system which include placing the vibration sensor on the intermediate mass, and the inherent stiffness of each component result in three critical implications for its uses in active floor vibration cancellation.
First, a piezo-based serial type system is the ideal choice for floor vibration isolation, particularly at very low frequencies. As commercially available nano-metrology and inspection tools become more sensitive to floor vibration, the need for low frequency floor vibration cancellation can be met only by a serial type, piezo based system, with an active bandwidth starting a 0.6Hz, with no inherent low frequency resonances. The next critical implication is that the control system does not detect payload motion, and thus stability and vibration cancellation performance of a serial type system is not affected by motion and resonances of the payload. It is inherently stable. This is because the sensor is placed on the intermediate mass which can easily be designed free of any low frequency resonances. The sensor is decoupled from the payload by the stiff elastomer mount, and is physically capable of detecting only floor vibration via the piezoelectric actuators. Therefore, the floor vibration measurement and subsequent feedback cancellation effort is not polluted by signals resulting from payload motion or resonances. The final implication of the serial configuration utilizing stiff passive springs and precision piezoelectric actuators is that the system total stiffness is very high, often referred to as a “hard mount” system. The primary advantage of a “hard mount” system is that “softer” systems, such as passive pneumatic or even active parallel pneumatic systems, can be “stacked” on the payload without the two systems coupling, due to a large separation in their resonant frequencies. Therefore, they lend themselves very well, with no additional tuning or customization, to payloads that include their own internal passive or active vibration cancellation systems, as nearly all modern nanotechnology tools have. “Hard mount” serial type systems also settle quickly after a payload disturbance. Their application in stage motion cancellation is best suited to tools with very high force moving stages which are impractical to cancel with linear motors due to the very high cancellation forces required. It is important to note that while the primary advantages of a serial type active vibration cancellation system over a parallel type system include superior performance at low frequencies, immunity from payload resonances, and ability to include additional isolation systems on the payload, the benefits are not limited to only low frequency performance. Serial type systems can maintain active vibration isolation up to 150Hz, and due to the additive performance of the serial passive component, they are able to provide low maintenance cancellation at a broad range of frequencies.
Serial type systems, when used in floor vibration cancellation applications, also require considerably less tuning than parallel type systems. The restriction of sensor location to the intermediate mass is superior to the use of two sensors which must be tuned to a happy medium between the earth and the payload as described above for parallel type systems. Without having to be carefully tuned specifically to the initial vibration conditions, serial type systems are less apt to fall out of tune, and require far less maintenance throughout the life of the system.
Parallel type systems, having sensors that detect payload motion, are an ideal choice for cancelling payload motion as a result of a known input. Serial type systems have no ability to act on the payload directly, but they also do not sense payload resonances. This makes them ideal for floor vibration cancellation, particularly at low frequencies when the serial type system is piezo-based. Although they do not actively cancel out stage motions, their “hard mount” architecture keeps settling time very low compared to passive systems, and their immunity to payload resonances ensures the feedback signal is accounting only for floor vibration, and enables serial type systems to be used with additional vibration isolation systems on the payload.